1. Problem: Slag Sprëtz
Am Prozess vum Laser-Schweißen sprëtzen d'geschmëlzene Material iwwerall an hält sech un d'Uewerfläch vum Material, sou datt Metallpartikelen op der Uewerfläch erscheinen an d'Schéinheet vum Produkt beaflossen.
D'Ursaach vum Problem: Spatzen kënnen duerch exzessiv Kraaft sinn, déi zu ze séier Schmelzen resultéiert, awer och well d'Materialfläch net propper ass oder de Gas ze staark ass.
Léisung: 1, entspriechend Muecht Upassung; 2, oppassen op d'Material Uewerfläch Botzen; 3, reduzéieren de Gas Drock.
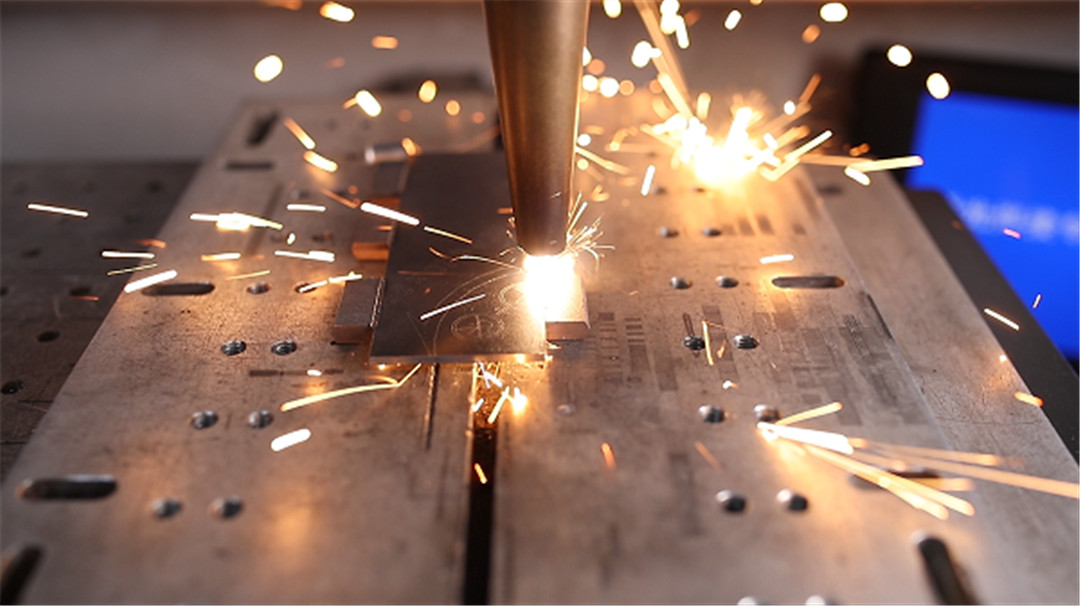
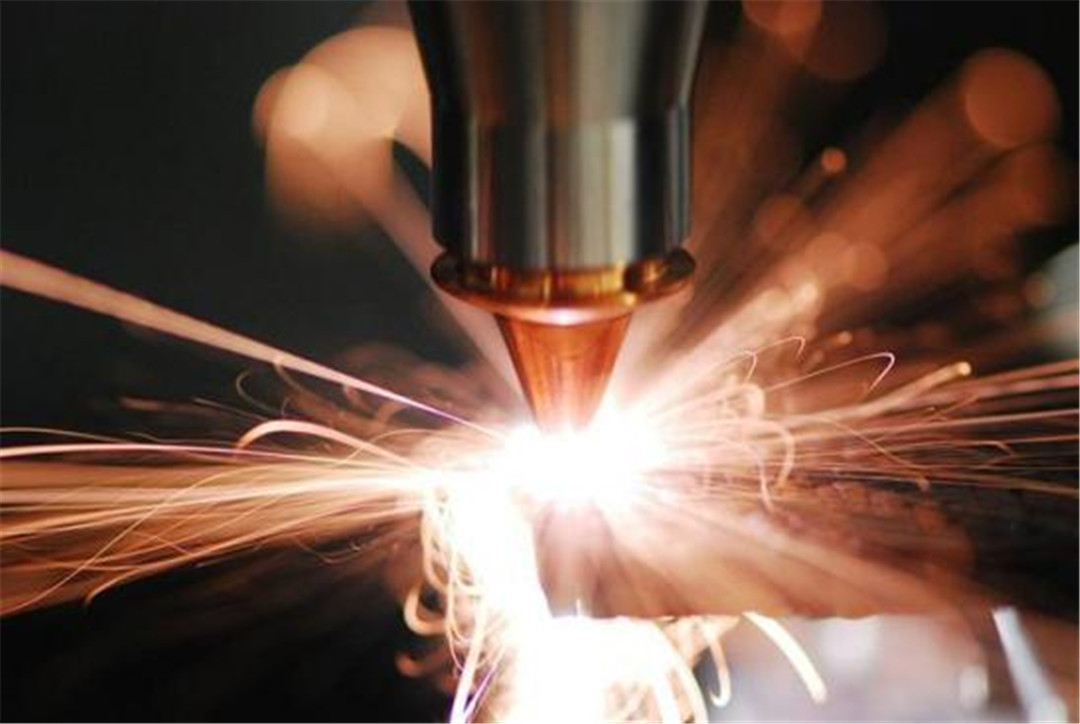
2. Problem: D'Schweißnaht ass ze héich
Schweess wäert feststellen datt d'Schweißnaht wesentlech méi héich ass wéi de konventionellen Niveau, wat zu engem Fettschweißnaht resultéiert, wat ganz onattraktiv ausgesäit.
De Grond fir de Problem: D'Draadfeedgeschwindegkeet ass ze séier oder d'Schweißgeschwindegkeet ass ze lues.
Léisung: 1. Reduzéieren der Drot fidderen Vitesse am Kontroll System; 2. Erhéije d'Schweißgeschwindegkeet.
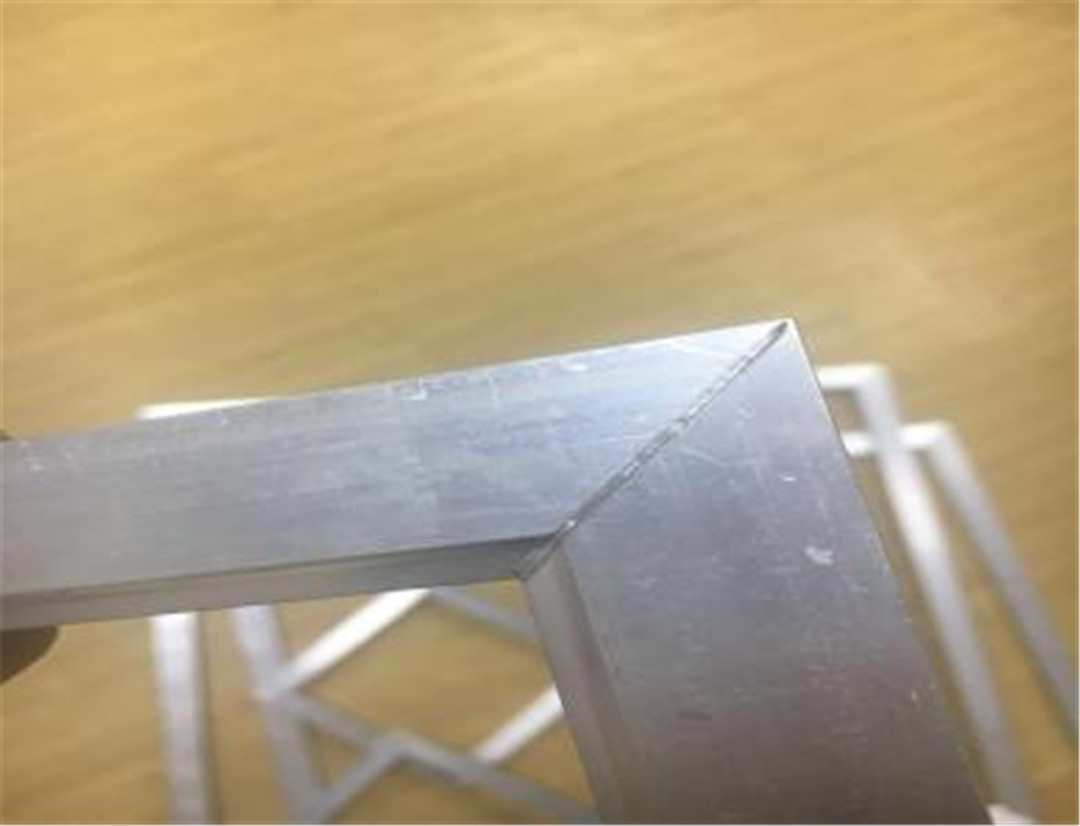
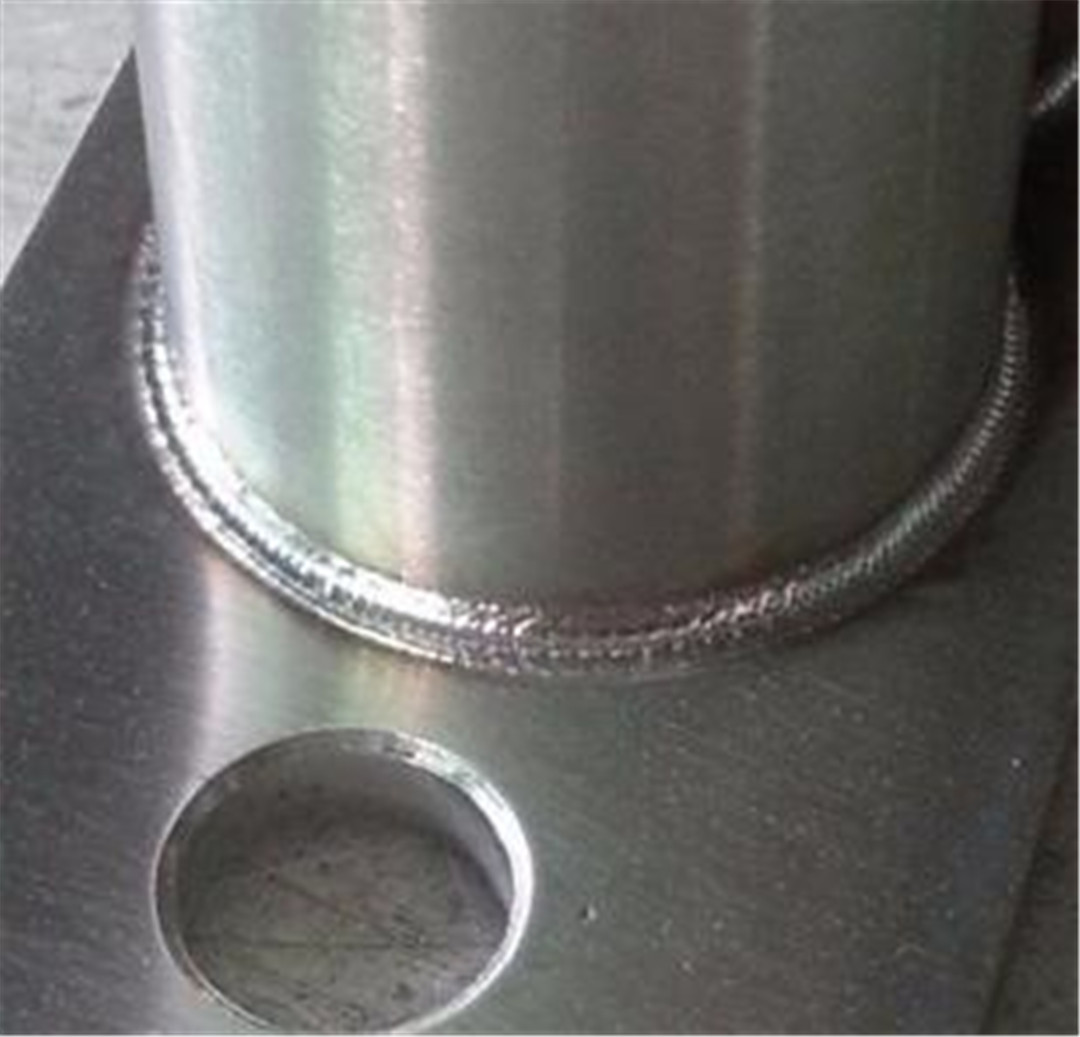
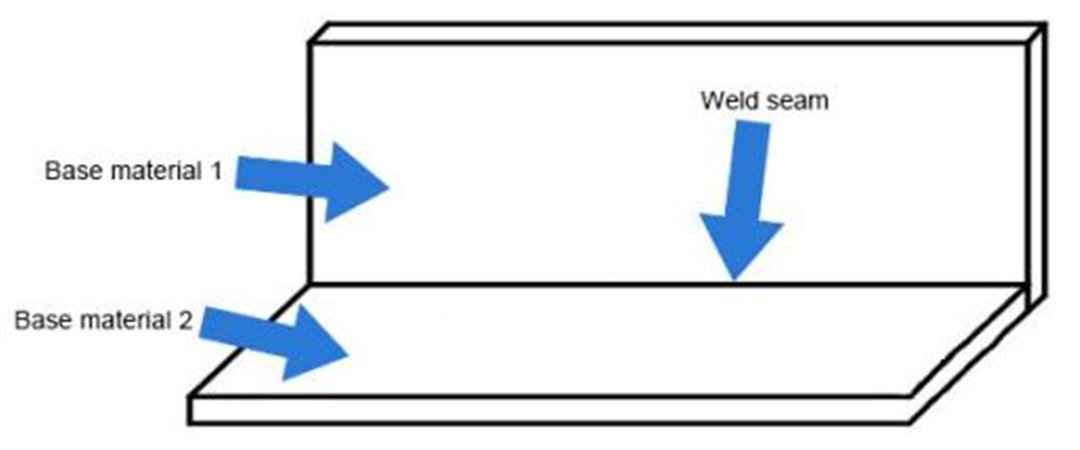
3. Problem: Schweess Offset
Schweißen ouni Verstäerkung an de strukturelle Gelenker an ongenau Positionéierung kënnen zu engem kompletten Ausfall vum Schweißen féieren.
Ursaach vum Problem: ongenau Positionéierung beim Schweißen; onkonsequent Positioun vun Drot fidderen an Laser Bestralung.
Léisung: 1. Ajustéieren der Laser Offset a Schwéngung Wénkel am Verwaltungsrot; 2. Kontrolléiert d'Verbindung tëscht dem Drotfeeder an dem Laserkopf fir Ofwäichung.
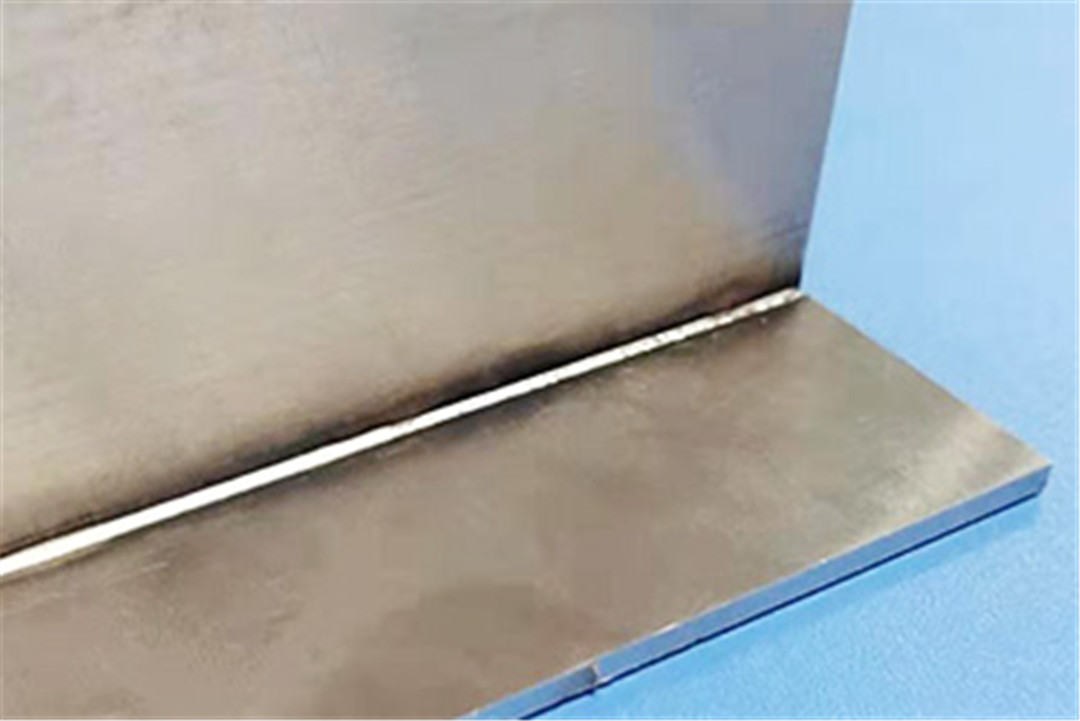
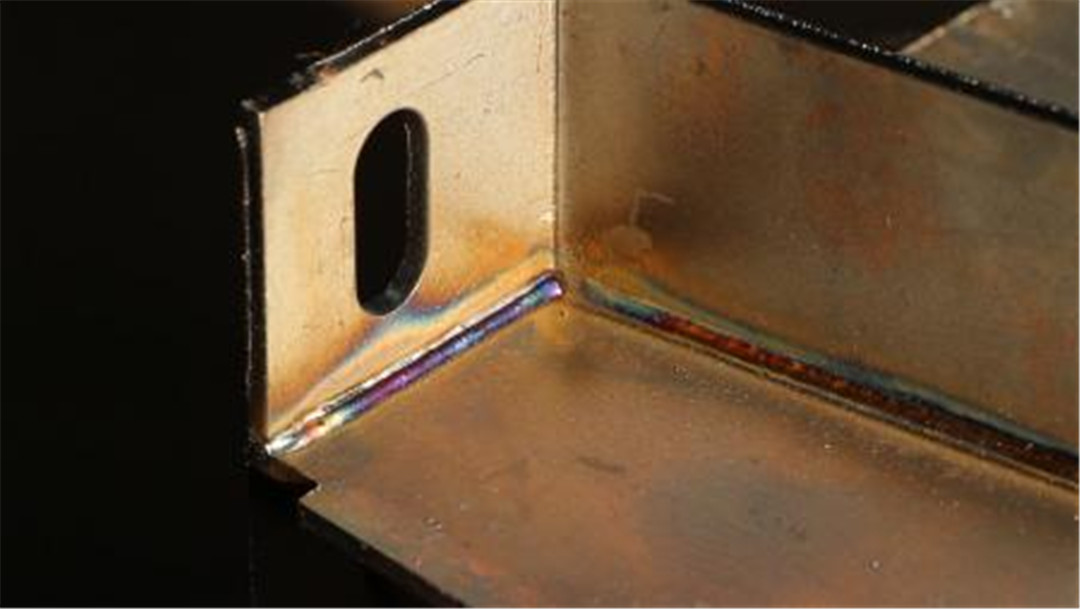
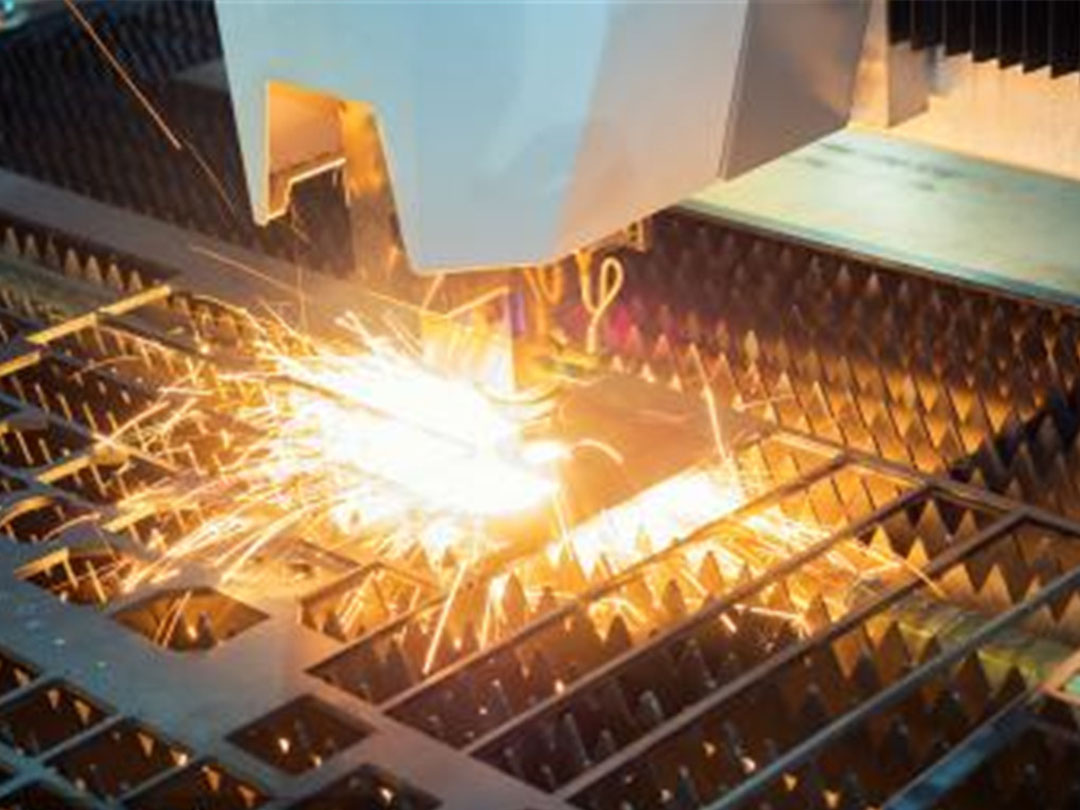
4. Problem: D'Faarf vum Schweiß ass ze däischter
Wann d'Schweißen Edelstahl, Aluminiumlegierung an aner Materialien, d'Schweißfaarf ze däischter ass, wäert d'Schweiß maachen an d'Materialfläche e staarken Kontrast produzéieren, extrem d'Schéinheet beaflossen.
De Grond fir de Problem: d'Laserkraaft ass ze kleng, wat zu net genuch Verbrennung resultéiert oder d'Schweißgeschwindegkeet ass ze séier.
Léisung: 1. ajustéieren der Laser Muecht; 2. ajustéieren der Schweess Vitesse.
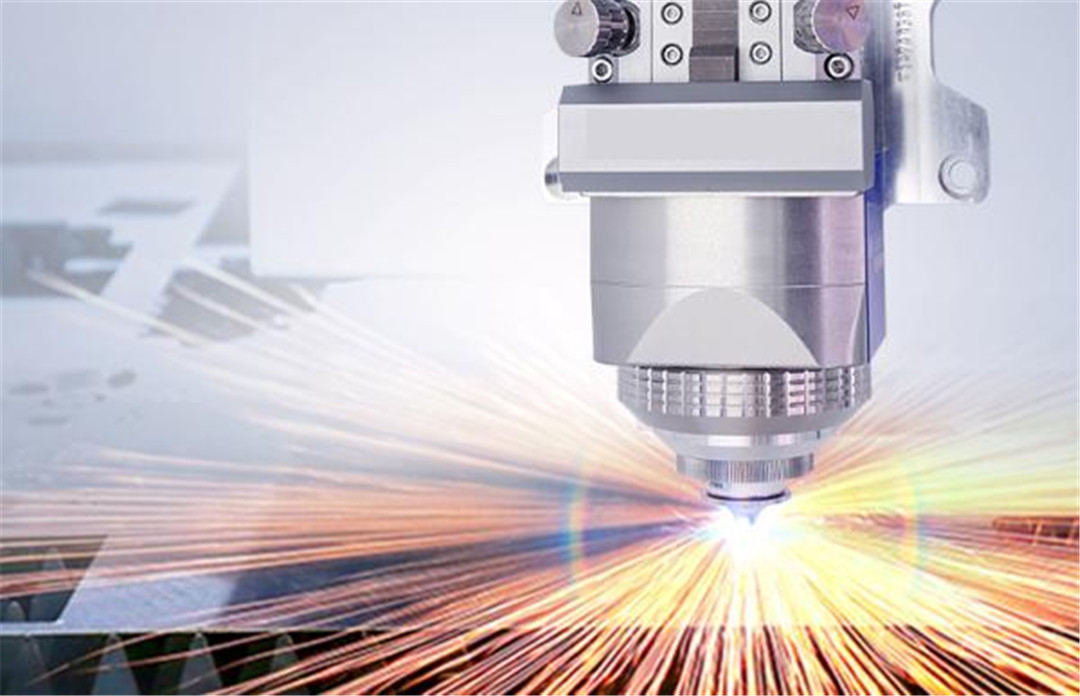
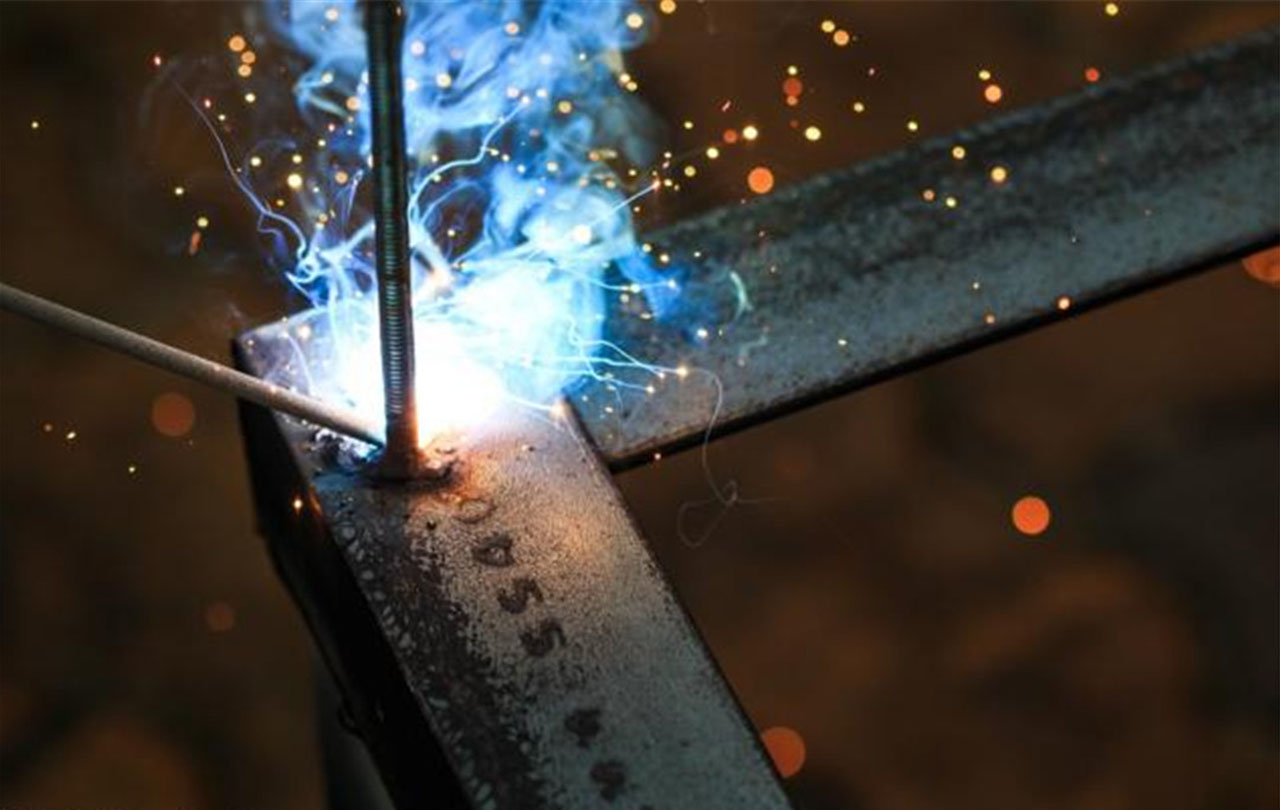
5. Problem: Ongläiche Corner Schweess molding
Beim Schweißen vun den bannenzegen an äusseren Ecken sinn d'Ecken net op d'Geschwindegkeet oder d'Haltung ugepasst, wat einfach zu ongläiche Schweißen an den Ecken féieren kann, souwuel d'Kraaft vum Schweißen an d'Schéinheet vum Schweißen beaflossen.
Ursaach vum Problem: onbequem Schweißhaltung.
Léisung: Ajustéiert de Fokus Offset am Laser Kontrollsystem sou datt den Handheld Laser Kapp Schweessoperatiounen op der Säit ausféiere kann.
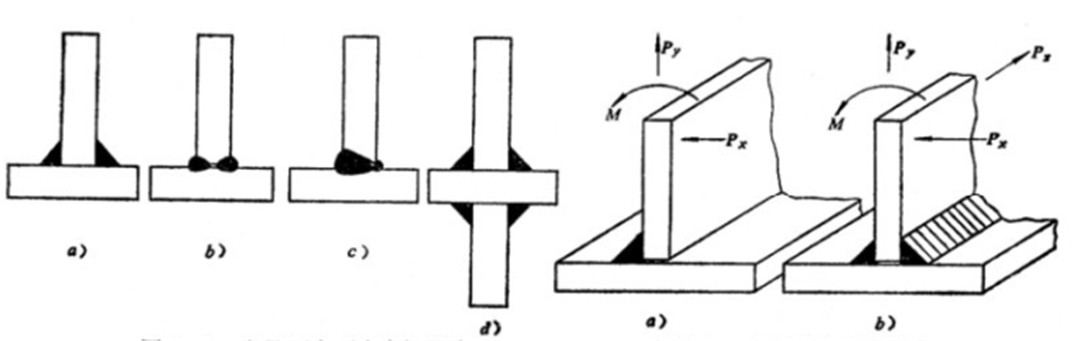
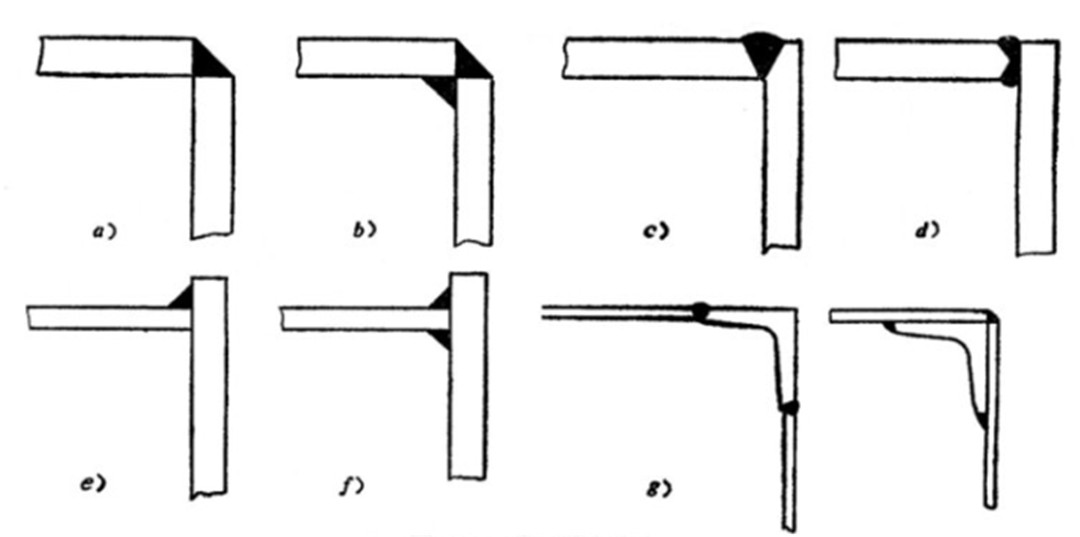
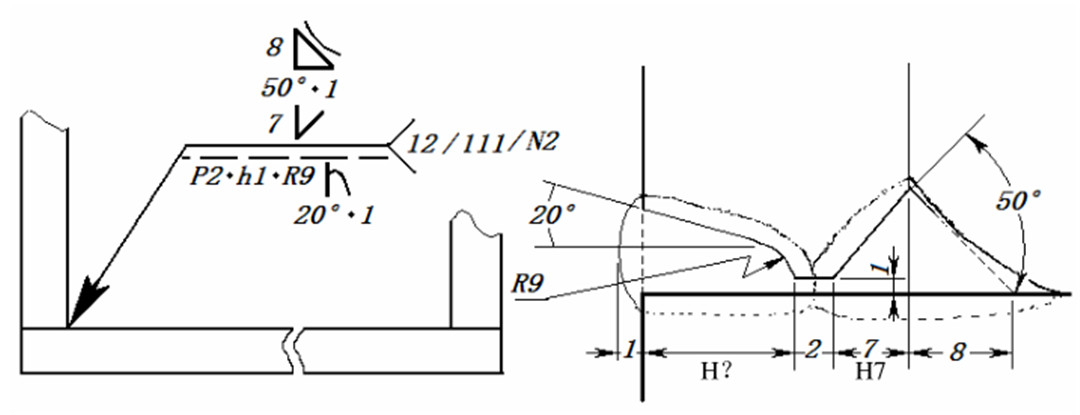
6. Problem: Schweess seam Depressiounen
Dents am geschweißte Gelenk féieren zu net genuch Schweißstäerkt an onqualifizéierte Produkter.
Ursaach vum Problem: D'Laserkraaft ass ze grouss, oder de Laserfokus ass falsch gesat, wat verursaacht datt de Schmelzpool ze déif ass an d'Material iwwerschmëlzt, wat am Tour zu der Schweessnahtdepressioun féiert.
Léisung: 1. Ajustéieren der Laser Muecht; 2. Ajustéieren der Laser konzentréieren.
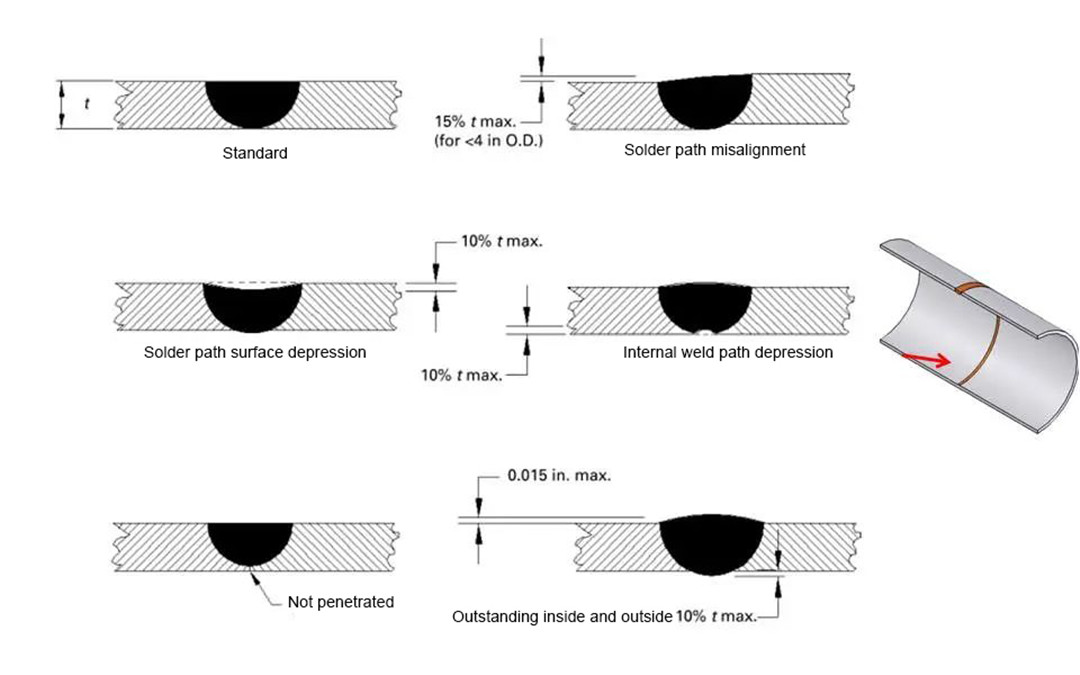
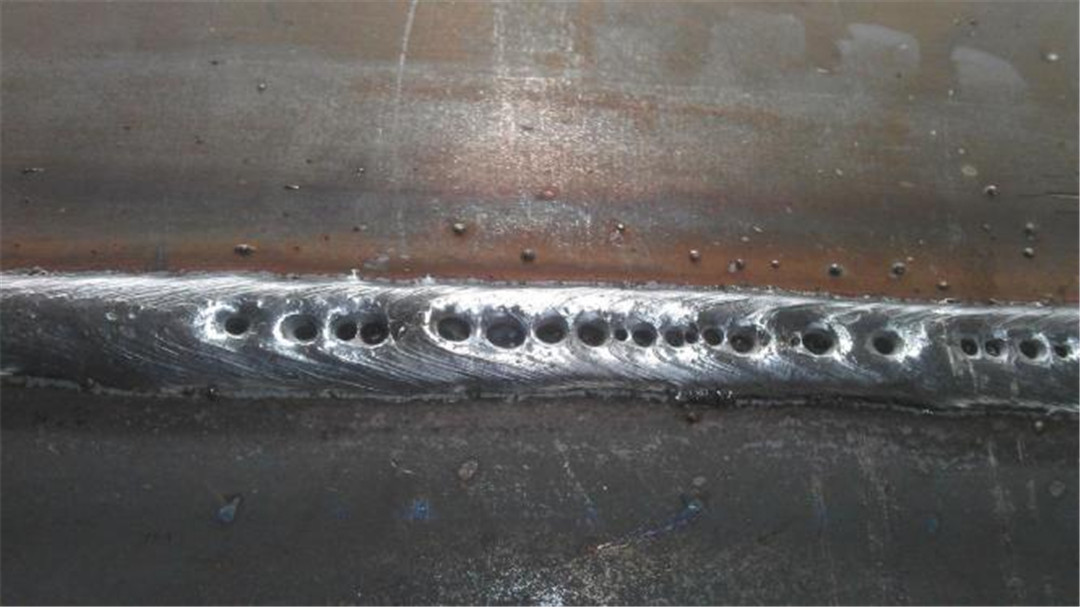
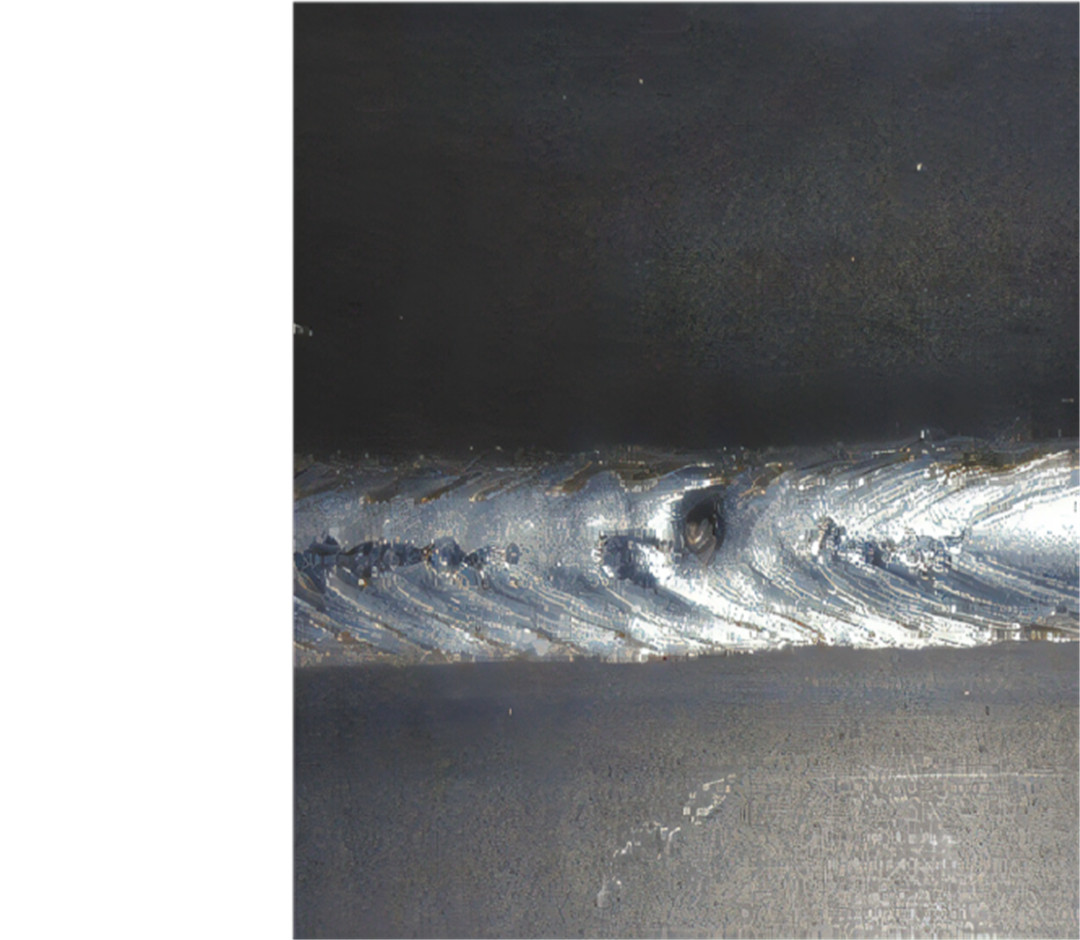
7. Problem: d'Schweißdicke ass net eenheetlech
Weld seam ass heiansdo ze grouss, heiansdo ze kleng, oder heiansdo normal.
Ursaach vum Problem: d'Luucht oder d'Draadfeed ass kee Problem.
Léisung: Iwwerpréift d'Stabilitéit vum Laser- an Drotfeeder, inklusiv Stroumversuergungsspannung, Killsystem, Kontrollsystem, Gronddrot, asw.
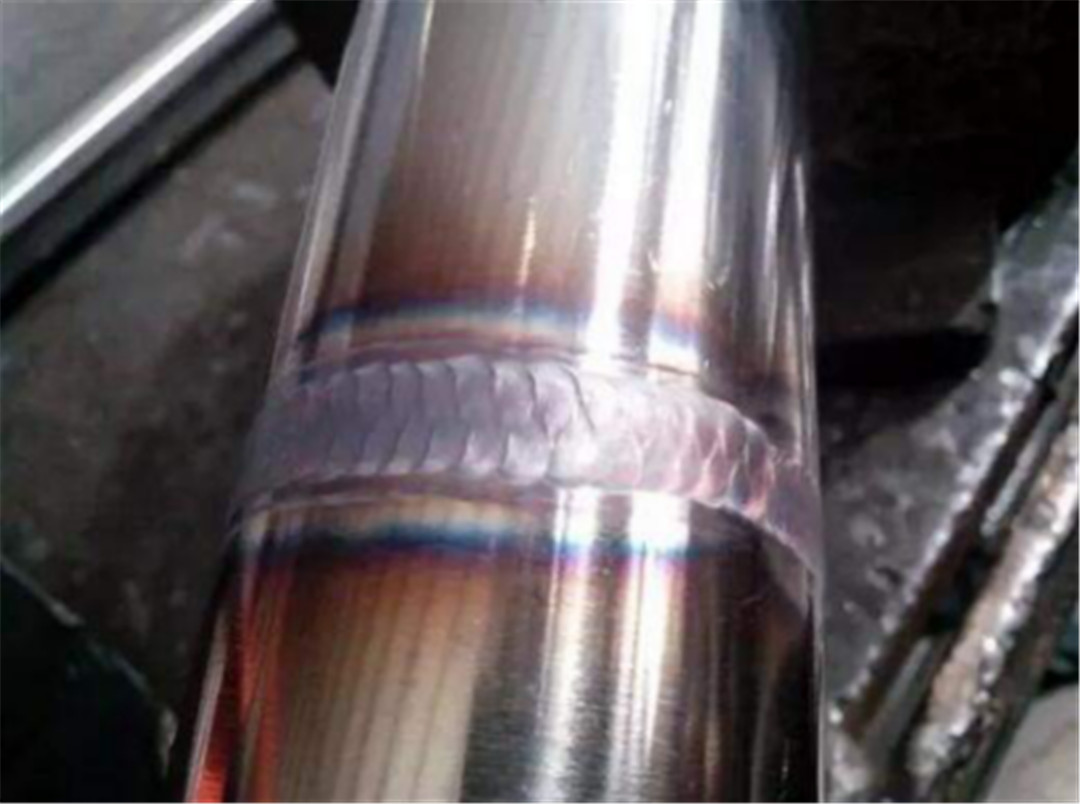
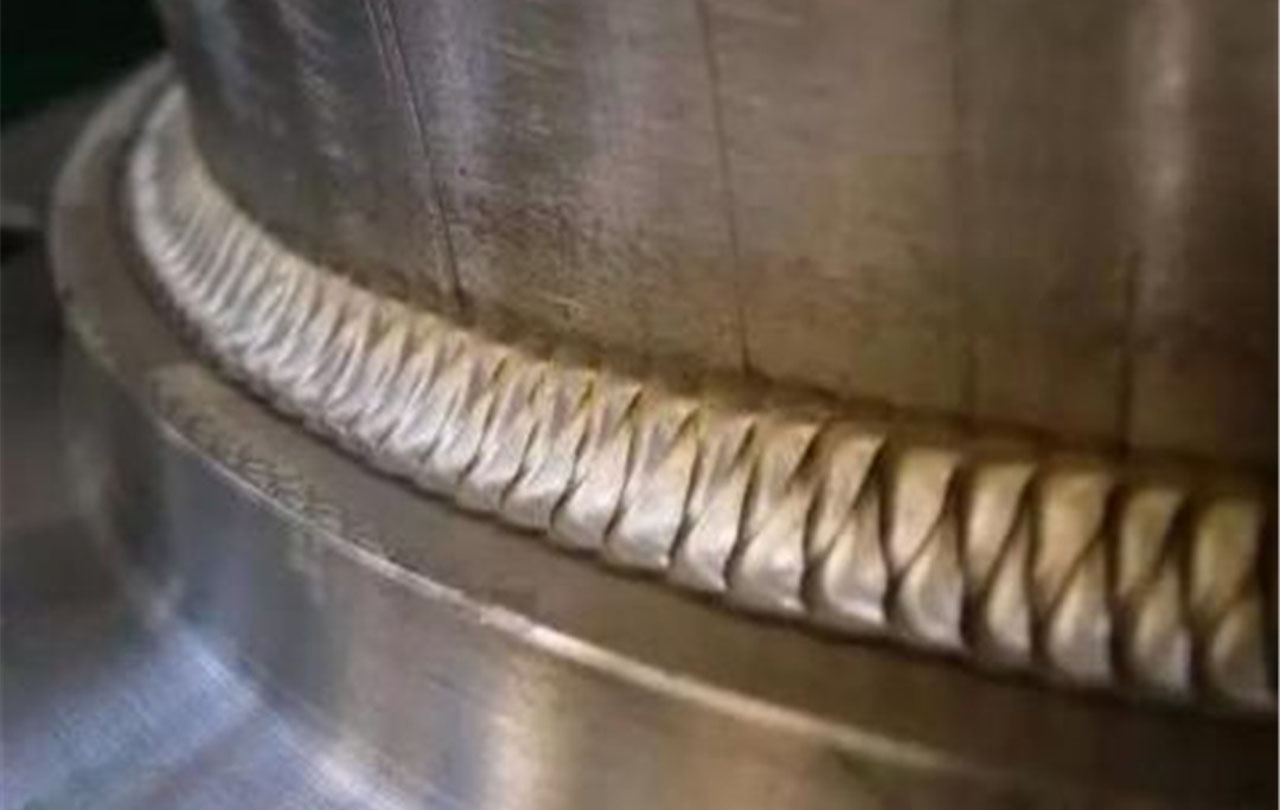
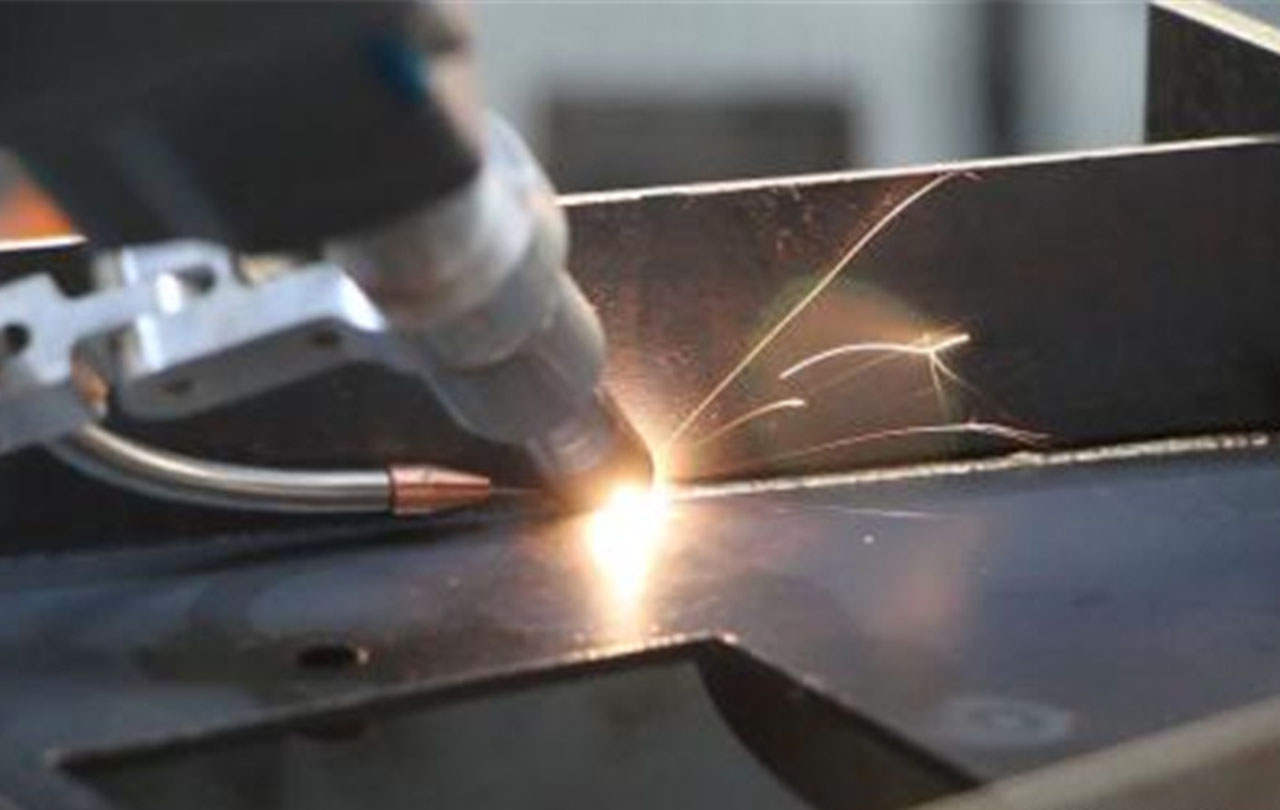
8. Problem: Bëssen Rand
Bite Rand bezitt sech op d'Schweiß an d'Material ass net gutt kombinéiert, Schräg an aner Konditiounen, also beaflosst d'Qualitéit vum Schweißen.
Ursaach vum Problem: Schweißgeschwindegkeet ass ze séier, wat doduerch datt de Schmelzpool net gläichméisseg op béide Säiten vum Material verdeelt ass, oder d'Materialspalt ass grouss, d'Füllmaterial ass net genuch.
Léisung: 1. Ajustéiert d'Laserkraaft an d'Geschwindegkeet no der Stäerkt vum Material an der Gréisst vun der Schweißnaht; 2. Fëllung oder Reparaturaarbechten spéider aus.
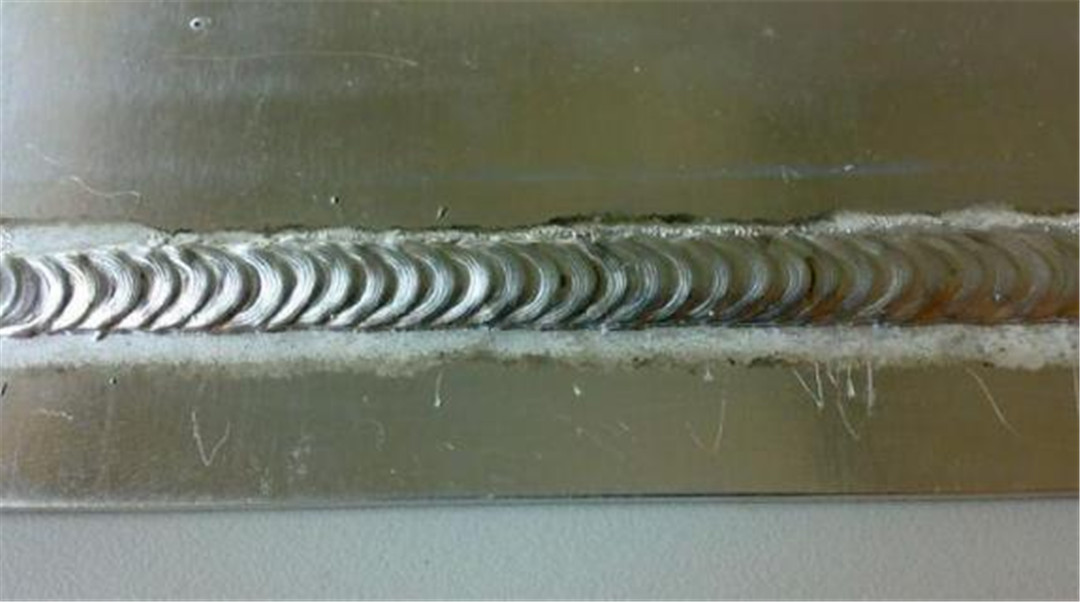
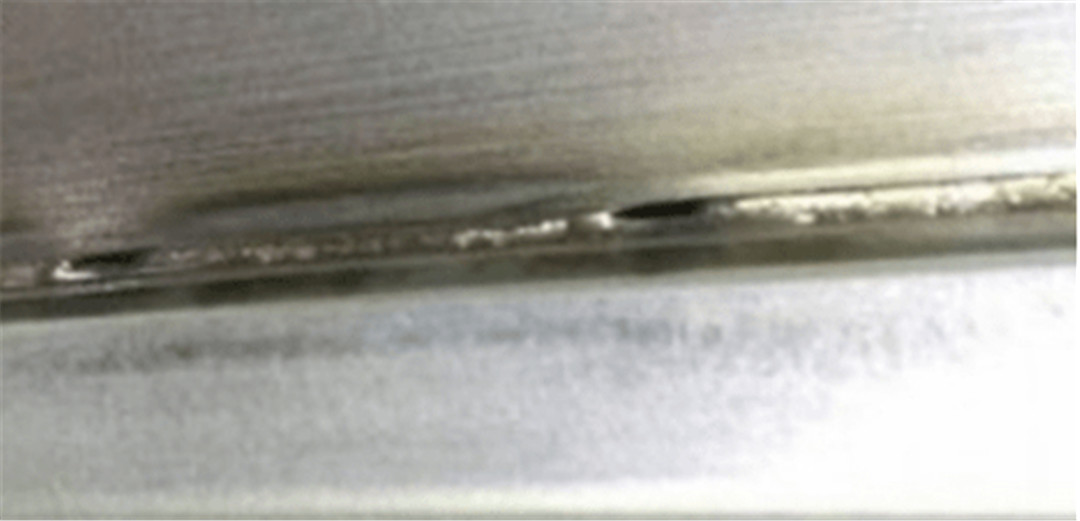
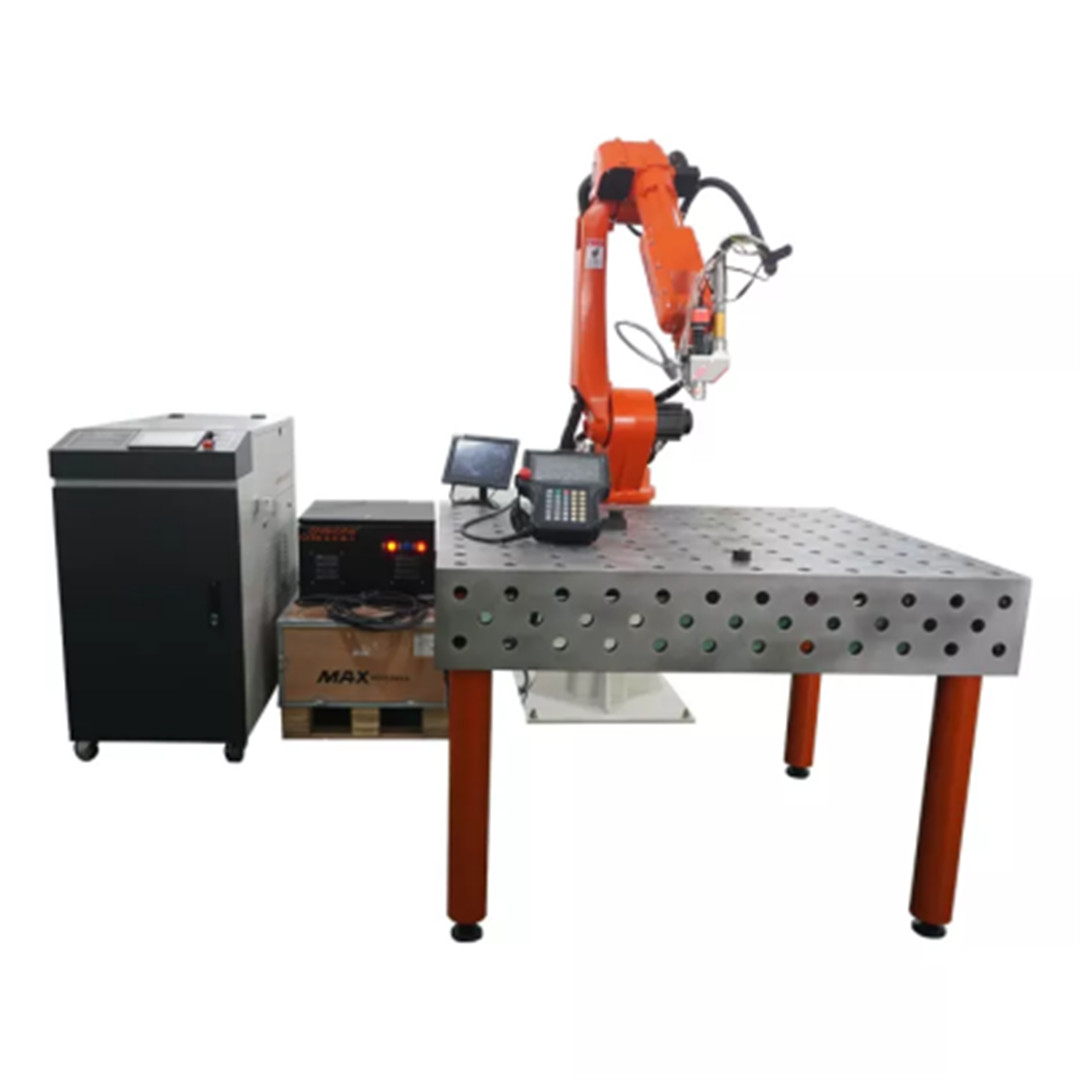
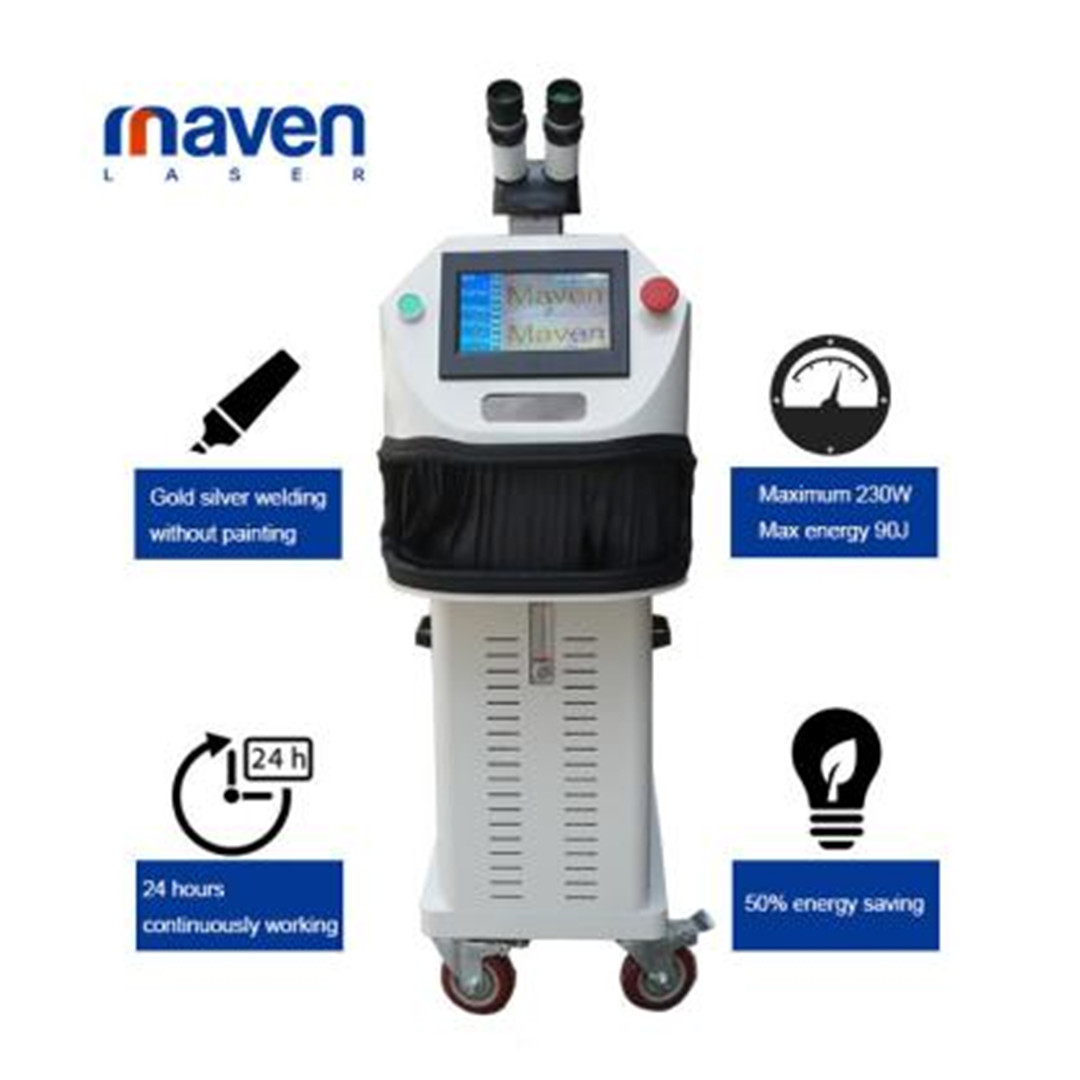
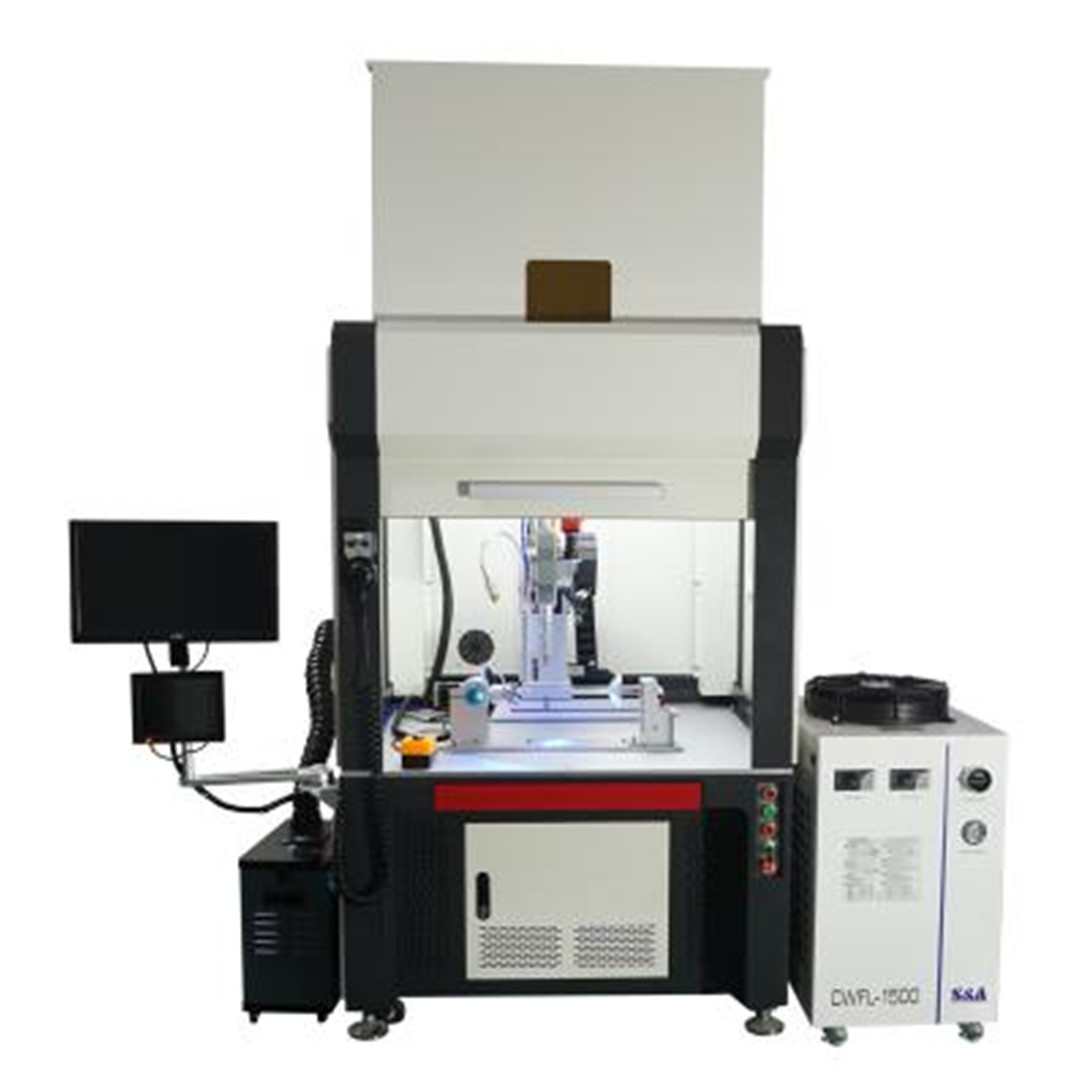
Maven Laser Automation Co.,Ltd. (Maven Laser kuerz) ass e féierende Fabrikant vu Lasersystemer a professionnelle Automatisatiounsléisungen, zu Shenzhen, China, gegrënnt am Joer 2008. Eis professionell Produkter sinn: Laserreinigungsmaschinn, Laser Schweessmaschinn, Roboter Schweessmaschinn a Plattform Schweessmaschinn, wann Dir hutt professionell Froen, wëllkomm eis ze konsultéieren.
Post Zäit: Nov-18-2022